On the history of East Asian porcelain and how it impacted on Meissen

China
The Chinese have mastered the art of pottery for over 4,500 years now. The manner in which porcelain was discovered in the 7th century owed something to chance, however. The evolution from a light-coloured fine stoneware to what was initially a greyish, not very translucent porcelain was fluid. Celadon ware from the Song Dynasties (960-1279) was the most highly regarded kind. Interest focused on formal factors. Relief-moulded patterns were incised, carved or impressed into the ceramic body. Various shades of green were adopted ranging von a watery leek-green to a bold bottle or glaucous green.
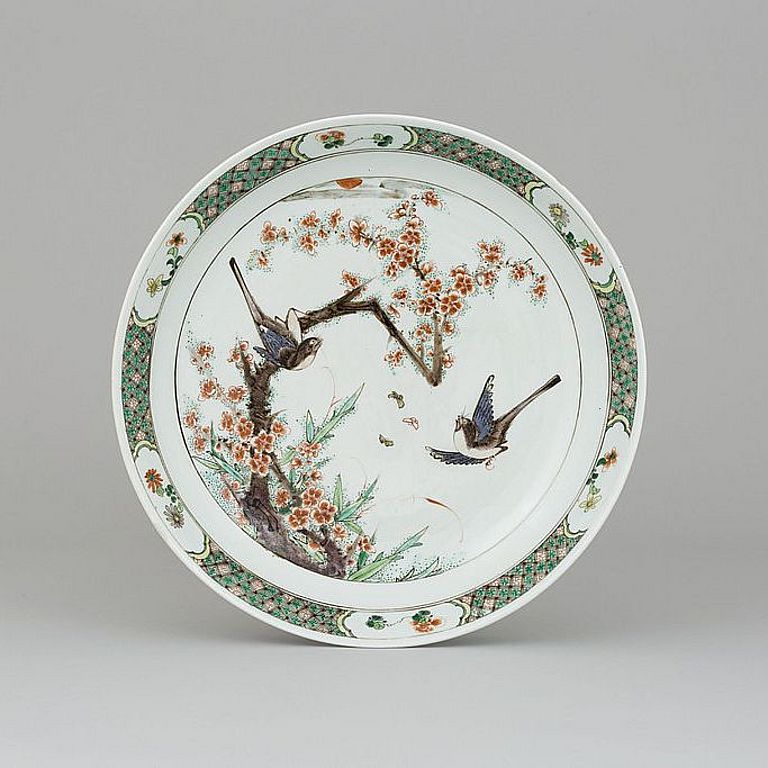
From the formal to the decorative
Under the influence of Mongol rule (1279-1368), interest shifted from formal to decorative attributes. It was the invention of decoration in underglaze cobalt blue, which was applied directly to the formed body once it had dried, that ushered in this change. Items were decorated with the likes of dragons, peony, chrysanthemum or stylised landscapes. The painted detail on ceramic ware first peaked in the 15th century. The kilns in Jingdezhen, strategically located close to the Yangtse River, led the way towards continuous production. Several trade routes intersected there at Jingdezhen. There was ample firewood with which to fuel the kilns, whilst the raw materials needed to make the ceramic ware were also to be found locally; red clay for the kilns, and both saggars and white clay for the ware. Thus it was that Jingdezhen became the ceramic centre for all China. A large number of decorative techniques were perfected during the Ming and Qing Dynasties (1368-1912) that had a profound impact upon Japanese and European art in the 18th century. Ongoing technical advances finally led to conveyor-belt-type mass production. The definitive stock of shapes and patterns for Chinese porcelain had been compiled by about 1800.
Paste and firing
Chinese porcelain consists of kaolin, feldspar and quartz. It is only fired once. High firing temperatures of between 1,250 and 1,300 degrees Centigrade cause material and glaze to fuse inseparably together. Porcelain long meant far less to the Chinese than it did to the Europeans. There was no separate word for it in Chinese. The term “Tz’u” evolved, which translates as high-quality stoneware with glaze. A distinction is made between earthenware, which is fired at approx. 600-800 degrees Centigrade, and stoneware, fired at 1,000-1,300 degrees Centigrade. Every type of ceramic is made up of two basic materials: the “silicates” - fluxing agents such as quartz, sand or feldspar that melt at high temperatures - and chalk, a weathering product of feldspar, granite, porphyry etc. that is malleable but does not melt. Fluxing agents melt at about 1,000-1,300 degrees Centigrade, causing stoneware to become as hard as stone and produce a clear sound when struck. Where the clays used contain sufficient silicates, i.e. fluxing agents, and little trace of metals, what comes out of the kiln will of necessity be porcelain.
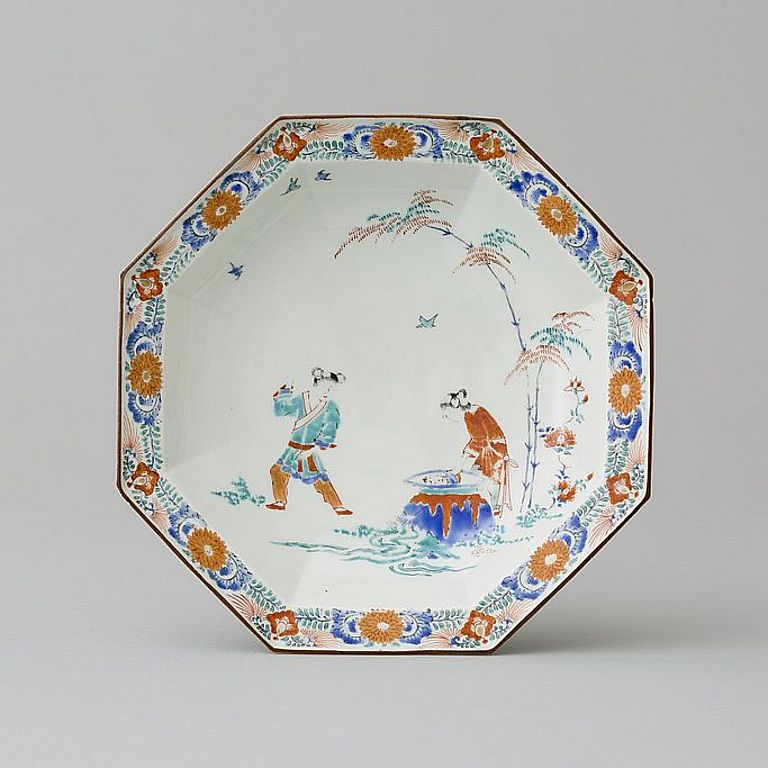
Japan
Japan and China have always engaged in cultural exchange, and yet Japan did not commence making porcelain until 1,000 years after the Chinese. No deposits of kaolin had been known of in Japan until the 17th century, when Korean potters discovered kaolin on Mount Izumiyama, not far from the small town of Arita. The potters had been abducted to Japan during that country’s invasion of Korea (1592-1598) and were settled in the north-west of the island of Kyushu. The first Japanese porcelains with decoration in underglaze cobalt blue came onto the market in 1616. The shapes and motifs they incorporated still clearly betrayed Korean influences. There followed porcelains that bore stronger echoes of the blue-and-white ware of the late Ming Dynasty (1368-1644). These various influences then merged with domestic stylistic elements to yield shapes and patterns that were distinctively Japanese. Popular uprisings verging on civil war in China resulted in exports of Chinese porcelain coming to a virtual halt in the mid-17th century. This conveniently opened the way for Japan’s fledgling porcelain industry to do business with the Dutch East Indies Company. Early Japanese porcelains were primarily exported as a consequence. Kakiemon and Imari brocade porcelains were particularly sought after.
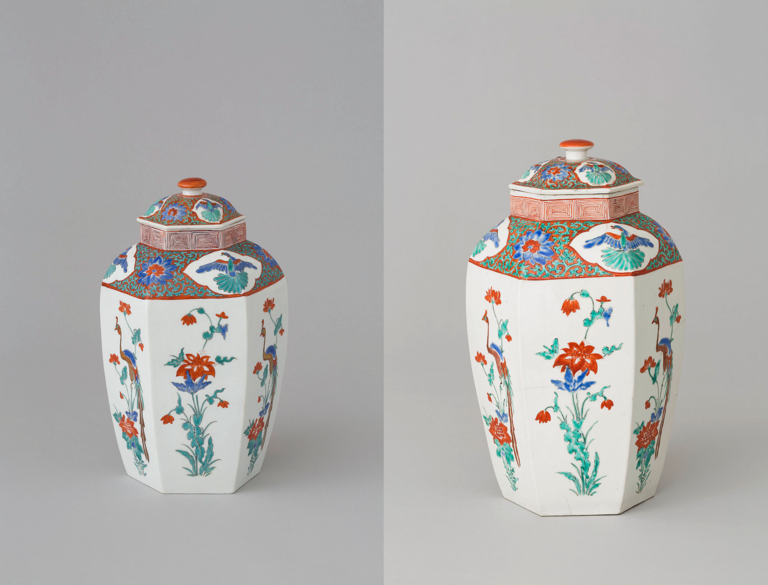
Influence on Meissen patterns
The majority of East Asian patterns that were copied at Meissen had their origins in multifarious dealings between porcelain manufacturers in Arita, Japanese intermediaries, Dutch (Delft) faience painters and the commissioning party, the Dutch East Indies Company. The latter had porcelains made in Arita to both Chinese and European models. The Chinese models featured Ming patterns that were specially adapted for the European market to suit Dutch tastes. The Japanese acquired a familiarity with European tastes in this way and proceeded to produce porcelains of their own for the export trade. The Dutch once again modified these Japanese export porcelains and in turn came up with new patterns of their own that were then used to decorate porcelains made in Arita. Strong demand for porcelains in the Kakiemon and Imari styles persisted into the first quarter of the 18th century on the Dutch market, whereupon the Company now had porcelain produced to Japanese patterns in China. In addition, Dutch painters decorated East Asian porcelain in the white in the Japanese style.